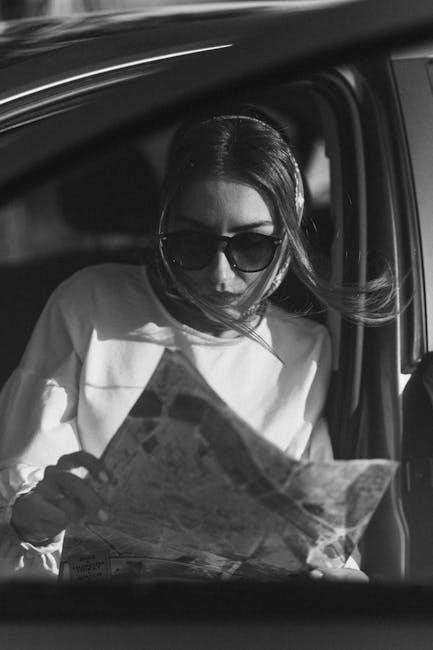
Classic Tailor Guide Article Plan
This comprehensive guide will explore the art of classic
tailoring. We’ll journey from essential tools to intricate
construction. Expect a deep dive into menswear techniques. Also,
discover tailoring’s role within WoW Classic. This guide offers
expertise for both beginners and seasoned crafters.
Classic tailoring represents a pinnacle of garment construction, emphasizing
precision, fit, and enduring style. Rooted in time-honored techniques, it
transcends fleeting trends, offering garments designed for longevity and
personalized comfort. Unlike mass-produced clothing, classic tailoring
prioritizes the individual, crafting pieces that reflect unique body shapes and
personal preferences. This approach involves meticulous handwork, careful
fabric selection, and a deep understanding of garment structure.
The essence of classic tailoring lies in its commitment to quality and
craftsmanship. Each step, from initial measurements to final finishing, is
executed with meticulous attention to detail. This results in garments that
not only fit impeccably but also possess a distinct character and elegance.
Whether it’s a bespoke suit, a tailored jacket, or a custom-made coat,
classic tailoring elevates clothing to an art form, transforming fabric into
lasting expressions of individual style. It’s a world where precision meets
artistry.
Fundamentals of Classic Tailoring
This section will explore the core principles. We will cover essential tools
and equipment needed for tailoring. Fabric selection is key, so we will
discuss the best choices. Mastering these fundamentals ensures successful
tailoring projects from start to finish.
Essential Tools and Equipment
Embarking on the journey of classic tailoring requires a carefully curated
arsenal of tools. Precision is paramount, so invest in high-quality
instruments. A sharp pair of tailoring shears is indispensable for clean fabric
cuts. Seam rippers are vital for correcting mistakes without damaging the
material. Measuring tapes and rulers ensure accurate dimensions are
maintained throughout the process.
Beyond cutting and measuring, hand-sewing needles are essential for delicate
stitches. Thimbles protect fingers during hand sewing. Pressing tools, such
as a tailor’s ham and sleeve board, mold fabric. Wax is needed for thread,
and beeswax is necessary for strengthening stitches. Proper lighting is
crucial for detailed work, so ensure an adequate workspace.
A reliable sewing machine is a cornerstone of any tailoring workshop.
Selecting the right machine is important for stitching seams and hems
efficiently. Specialized feet, such as a zipper foot and buttonhole foot,
expand the machine’s capabilities.
Finally, don’t overlook the importance of a well-organized workspace. Storage
solutions keep tools accessible and prevent clutter. Maintaining equipment
prolongs their lifespan and ensures consistent performance.
Fabric Selection for Classic Garments
Choosing the right fabric is paramount to crafting timeless, classic
garments. The selection process depends on the garment’s style, intended use,
and desired drape. Wool, renowned for its durability and elegant texture, is
a staple for tailored suits and overcoats. Linen, a breathable and
lightweight option, exudes relaxed sophistication in summer attire.
Cotton, versatile and easy to maintain, lends itself to a range of garments,
from shirts to casual jackets. Silk, prized for its luxurious sheen and
smoothness, elevates formal wear and delicate blouses. Consider the fabric’s
weight, weave, and fiber content to ensure it aligns with the design.
For structured garments like jackets, heavier fabrics with a tighter weave
provide support and shape retention. Looser weaves, such as tweed or flannel,
impart a softer, more relaxed feel. Pay attention to the fabric’s drape, as
it influences how the garment hangs and moves.
Ultimately, fabric selection is a balance of aesthetics and functionality.
Carefully consider the fabric’s properties and how they contribute to the
overall vision of the classic garment.
Core Techniques in Classic Tailoring
Mastering core techniques is vital for classic tailoring. These
techniques include precise pattern preparation, meticulous hand stitching,
and skillful sewing machine operation. These form the basis for creating
well-fitted, durable, and aesthetically pleasing garments.
Pattern Preparation and Cutting
Accurate pattern preparation and cutting are critical first steps in
classic tailoring, influencing the final garment’s fit and appearance;
Start by carefully selecting the correct pattern size, considering
precise body measurements. Transfer the pattern onto the chosen fabric,
ensuring it aligns with the grainline for optimal drape and structure.
Use weights or pins to secure the pattern, preventing shifts during
cutting. Employ sharp shears or a rotary cutter for clean, precise cuts,
following pattern lines exactly—precision is key, like following a trail
where straying leads to obstacles. Mark all notches, darts, and other
construction details clearly.
Consider adding seam allowances according to the pattern instructions,
typically around 5/8 inch, to facilitate adjustments during fitting. Stay
stitching along curved edges prevents stretching and distortion. Handle
cut pieces with care, storing them flat or hanging to avoid wrinkles.
Accurate cutting is the cornerstone of successful tailoring.
Prioritize precision to ensure that the garment assembles smoothly and
fits impeccably. Proper preparation at this stage sets the foundation for
a professional and well-crafted tailored piece.
Hand Stitching Techniques
Hand stitching is a cornerstone of classic tailoring, offering precision
and control unmatched by machine sewing. Mastering these techniques is
essential for achieving a truly bespoke finish. The humble running stitch
forms the basis for many other stitches, used for basting layers of fabric
together temporarily. The back stitch creates a strong, secure seam,
ideal for areas requiring durability.
The slip stitch, almost invisible, is perfect for hemming and attaching
linings, ensuring a clean and polished look. Pad stitching, used in
lapels and collars, provides shape and structure, shaping the fabric with
rows of small, dense stitches. The pick stitch, a decorative yet
functional stitch, adds a subtle texture along edges and seams.
Each stitch requires practice to perfect, focusing on even tension and
consistent stitch length. Selecting the right needle and thread is
crucial; finer fabrics demand finer needles and threads. Hand stitching
not only enhances the garment’s appearance but also allows for greater
control, resulting in a superior fit and finish. It remains a vital part
of bespoke tailoring.
Despite the efficiency of sewing machines, about 75% of stitches in a
custom-tailored suit are traditionally done by hand.
Sewing Machine Techniques
While hand stitching offers unparalleled control, sewing machines are
indispensable for efficiency in classic tailoring. Mastering various
machine techniques is essential for constructing durable and professional
garments. A straight stitch is the workhorse, used for seams, darts, and
general construction. Experiment with stitch length to suit the fabric;
shorter stitches for delicate fabrics and longer stitches for heavier
ones.
Zigzag stitches are valuable for finishing raw edges, preventing fraying
and adding reinforcement. Overlock or serger machines create a clean,
professional edge, encasing the fabric to prevent unraveling. Blind hem
stitches create nearly invisible hems, perfect for tailored trousers and
skirts. Buttonholes, a crucial element, require specialized machine
settings or attachments to achieve a polished finish.
Consistent seam allowances are essential for accurate construction, using
the machine’s guide foot or markings on the needle plate. Pressing seams
open or to one side after stitching is crucial for a flat, professional
finish. Regular machine maintenance, including cleaning and oiling,
ensures optimal performance and longevity. Sewing machines are vital for
efficiency in tailoring, but mastering them takes time and dedication.
The sewing machine is used for almost all seams and darts in tailoring.
Construction Guide for Menswear
This section provides a detailed guide to menswear construction. We’ll
explore tailored jackets, focusing on collars and lapels. Expect
step-by-step instructions, perfect for both aspiring and experienced
tailors. Master the art of crafting exceptional garments.
Constructing a Tailored Jacket
The tailored jacket stands as a pinnacle of classic menswear, demanding
precision and skill. This section provides a detailed, step-by-step
guide to constructing one. First, selecting the appropriate fabric is
crucial, influencing the drape and structure of the jacket. Next, pattern
preparation involves meticulous cutting and marking, ensuring accuracy in
every piece.
The construction process begins with assembling the jacket’s body, paying
close attention to seam alignment and smooth transitions. Hand-stitching
techniques, such as pad-stitching and edge-stitching, add refinement and
durability. Sewing machine techniques are employed for efficiency,
especially in areas like lining attachment. Creating the jacket’s
structure involves careful interfacing and shaping. The shoulders, in
particular, require precise padding and shaping to achieve the desired
silhouette.
Attention to detail is paramount throughout the process. Proper pressing
techniques are essential to mold and set the fabric, creating sharp lines
and a polished finish. Finally, the finishing touches, such as buttonholes
and pocket placement, elevate the jacket’s overall quality. Mastering
these steps will enable you to craft a timeless, well-fitted tailored
jacket.
Creating Collars and Lapels
Collars and lapels are defining features of a tailored jacket, demanding
precision. Their construction significantly impacts the garment’s overall
aesthetic. This section guides you through creating these crucial
elements, focusing on techniques for achieving a professional finish.
First, pattern drafting is key, requiring accurate measurements and an
understanding of the desired shape and proportions. The collar’s stand and
fall must be carefully calculated to ensure it sits correctly on the neck.
Interfacing plays a crucial role in providing structure and support. Different
types of interfacing can be used to achieve varying degrees of stiffness
and drape. The lapel’s shape is determined by the break point and the
roll line, each needing precise manipulation. Hand-stitching techniques,
such as pad-stitching, are essential for shaping the lapel and creating a
smooth, controlled curve.
The collar and lapel are then attached to the jacket with meticulous
attention to detail. Under-collars and facings are carefully aligned and
sewn to ensure a clean finish. Pressing techniques are vital for molding
the collar and lapel into their final form, creating sharp edges and
defined lines. Mastering these techniques will result in collars and
lapels that enhance the jacket’s style.
Tailoring in WoW Classic
Explore Tailoring within the world of WoW Classic, a profession interwoven
with gameplay. Discover leveling strategies from 1-300. Learn about
essential pairings with Enchanting. Uncover recipes, materials, and the
creation of cloth armor.
Leveling Tailoring in WoW Classic (1-300)
Embarking on the Tailoring journey in WoW Classic requires dedication and
resourcefulness. This guide provides a pathway to reach skill level 300;
Start by training as an Apprentice at level 5. Then, systematically craft
items to advance your skill. Early levels involve creating basic cloth
items. Linen Cloth is fundamental in the initial stages. As you progress,
seek out new patterns from trainers. Also, consider exploring vendors for
unique recipes.
Wool Cloth becomes essential as you approach the mid-levels. Silk and
Mageweave Cloth follow, demanding efficient farming strategies. Locate
areas with high mob density to maximize cloth collection. Don’t forget to
visit Moonwells for Mooncloth creation, if applicable. This advanced
material is crucial for high-end recipes. Tailoring often pairs well with
Enchanting. Disenchanting crafted items provides valuable materials.
Remember, gold management is key. Selling crafted goods can offset the
cost of materials. This ensures a smooth leveling experience. Finally,
consider joining a guild. Guilds provide support and access to resources.
Tailoring and Enchanting Pairings
The synergy between Tailoring and Enchanting in WoW Classic is a powerful
combination. Tailoring creates cloth armor and bags, while Enchanting
enhances gear and provides valuable materials. This pairing creates a
self-sustaining cycle. Tailors can craft items specifically to be
disenchanted. This provides Enchanting materials, eliminating reliance on
the Auction House.
Unwanted crafted gear becomes a source of arcane dust and shards. These
materials are essential for enchanting recipes. Leveling both professions
simultaneously maximizes efficiency. Tailoring provides items for
Enchanting to break down. Enchanting, in turn, can improve the gear
Tailoring produces. This creates a beneficial loop for character
progression.
Furthermore, certain Enchanting recipes require materials obtained through
Tailoring. For example, specific cloth types or crafted items might be
needed. This interdependence strengthens the bond between the two
professions. Players who invest in both gain significant economic
advantages. They can craft, enchant, and sell high-demand items. Ultimately,
the Tailoring and Enchanting pairing offers a well-rounded approach to
character enhancement and resource management.